Glass manufacturing is a complex process that requires precision, attention to detail, and adherence to strict quality control measures to produce glass products that meet industry standards for consistency, performance, and safety. Quality control plays a crucial role in every stage of glass production, from raw material selection to the final inspection of finished products. This article explores the importance of quality control in glass manufacturing and the measures implemented to uphold standards across the industry.
Introduction to Quality Control in Glass Manufacturing
Quality control in glass manufacturing involves monitoring and maintaining standards throughout the production process to ensure that the final products meet predetermined criteria for performance, durability, and safety. This process encompasses various stages, including raw material testing, glass melting, forming, annealing, tempering, and inspection.
Raw Material Selection and Testing
One of the first steps in glass manufacturing is the selection and testing of raw materials. High-quality glass requires high-quality ingredients, including silica sand, soda ash, limestone, and other additives. These raw materials undergo rigorous testing to assess their chemical composition, purity, and suitability for glass production. Standards for raw material quality are established by industry organizations and regulatory bodies to ensure consistency and reliability.
For example, the International Organization for Standardization (ISO) sets standards for the chemical composition and physical properties of glass raw materials, such as ISO 336:1975 for soda ash and ISO 3262-19:2000 for silica sand. These standards provide guidelines for manufacturers to evaluate the quality of raw materials and maintain consistency in glass production.
Glass Melting and Forming
Once the raw materials are approved for use, they are mixed in precise proportions and melted in furnaces at high temperatures. The molten glass is then formed into the desired shape using various techniques, such as blowing, pressing, or drawing. During this stage, quality control measures are implemented to monitor the viscosity, temperature, and homogeneity of the glass melt to ensure uniformity and quality.
Automated monitoring systems and sensors are often used to measure key parameters, such as glass temperature, viscosity, and chemical composition, in real-time. Any deviations from the specified parameters can indicate potential quality issues and prompt corrective actions to maintain consistency and product integrity.
Annealing and Tempering
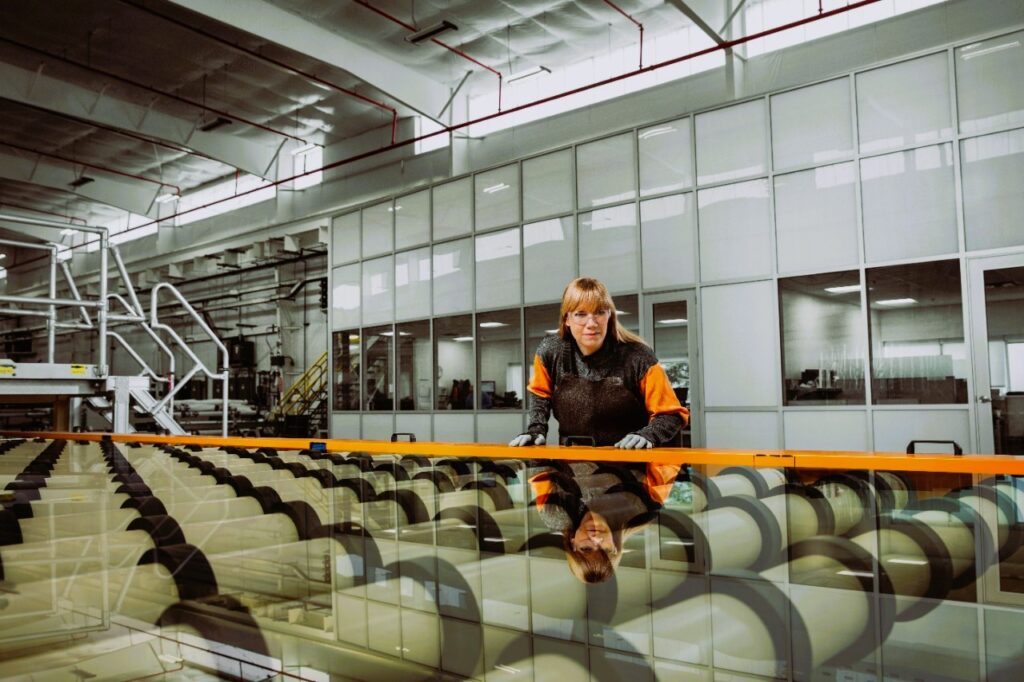
After forming, glass products undergo annealing to relieve internal stresses and improve strength and durability. Annealing involves gradually cooling the glass at a controlled rate to prevent cracking or distortion. Tempering is another process used to enhance the strength of glass by heating it to high temperatures and then rapidly cooling it. Both annealing and tempering are critical steps in glass manufacturing, and quality control measures are employed to ensure that the glass products meet safety standards and performance requirements. Do you like the article? We recommend reading about the Evolution of architectural glass.
Inspection and Testing
The final stage of quality control in glass manufacturing involves inspection and testing of finished products to verify their quality, performance, and safety. This may include visual inspection, dimensional measurement, surface quality assessment, and mechanical testing. Additionally, specialized tests, such as impact resistance, thermal shock resistance, and chemical durability tests, may be conducted to evaluate specific properties of the glass.
Industry organizations, such as the American Society for Testing and Materials (ASTM) and the International Commission on Glass (ICG), develop standards and test methods for assessing the quality and performance of glass products. For example, ASTM C1036 specifies the requirements for flat glass products, including annealed, heat-strengthened, and tempered glass, while ASTM C1048 outlines the requirements for heat-treated flat glass.
Conclusion
Quality control is paramount in glass manufacturing to ensure that the products meet stringent standards for consistency, performance, and safety. By implementing rigorous quality control measures throughout the production process, glass manufacturers can uphold the reputation of their brands, meet customer expectations, and contribute to the advancement of the industry as a whole.
For more information on glass manufacturing standards and quality control measures, please visit Wikipedia.