Glass manufacturing has undergone significant transformations over the years, driven by advancements in technology, changing consumer preferences, and evolving environmental regulations. As we look towards the future, several trends and innovations are poised to reshape the glass manufacturing industry, paving the way for more sustainable, efficient, and versatile production processes. In this article, we will explore some of the key trends and innovations that are shaping the future of glass manufacturing and their potential implications for the industry.
1. Sustainable Practices
One of the most prominent trends in glass manufacturing is the growing emphasis on sustainability and environmental responsibility. With increasing concerns about climate change and resource depletion, glass manufacturers are exploring ways to minimize their environmental footprint and reduce energy consumption throughout the production process. This includes investing in renewable energy sources, such as solar and wind power, implementing recycling programs to reduce waste, and adopting more efficient manufacturing techniques that require fewer raw materials and energy inputs. By embracing sustainable practices, glass manufacturers can not only reduce their environmental impact but also enhance their brand reputation and appeal to environmentally conscious consumers.
2. Advanced Materials
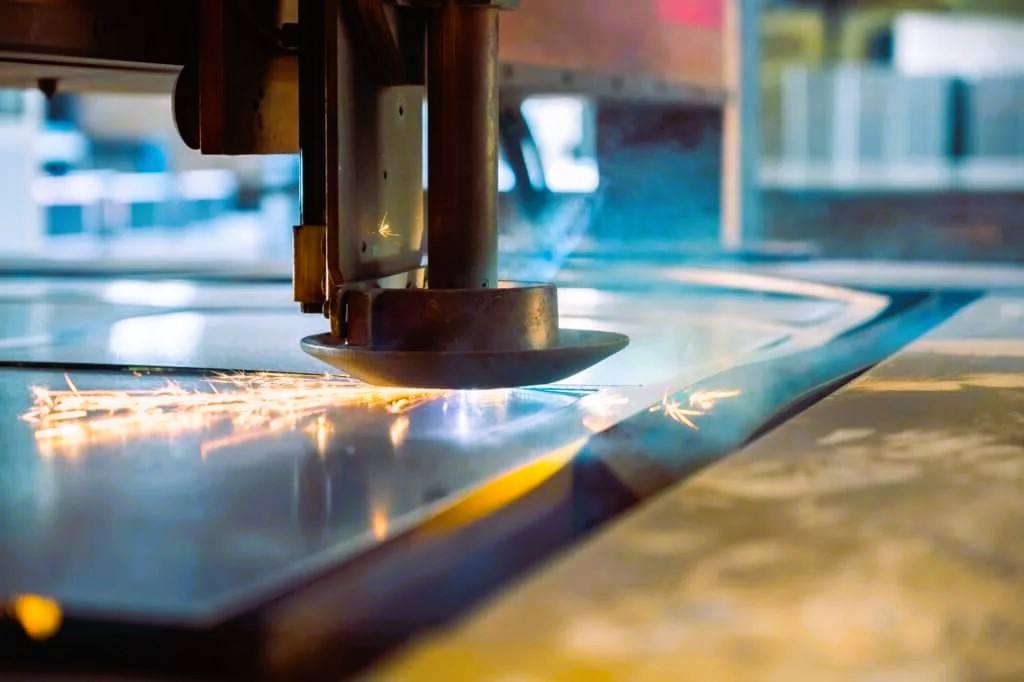
Another key trend in glass manufacturing is the development of advanced materials and coatings that offer enhanced performance and functionality. From self-cleaning and anti-fog coatings to conductive and smart glass technologies, manufacturers are constantly innovating to meet the evolving demands of various industries and applications. Advanced materials can improve the durability, strength, and thermal performance of glass products, making them suitable for a wide range of uses, including automotive, architectural, and electronics. By incorporating advanced materials into their products, glass manufacturers can differentiate themselves in the market and unlock new opportunities for growth and innovation. The art of glass etching, read more at this link.
3. Digitalization and Automation
Digitalization and automation are revolutionizing the way glass manufacturing processes are designed, operated, and optimized. By leveraging data analytics, artificial intelligence, and robotics, manufacturers can streamline production workflows, increase efficiency, and minimize errors and defects. Digital twin technology, which involves creating virtual replicas of physical manufacturing systems, enables real-time monitoring and predictive maintenance, allowing manufacturers to identify and address potential issues before they escalate. Automation also reduces labor costs and improves workplace safety by minimizing human intervention in hazardous or repetitive tasks. As digitalization and automation continue to advance, glass manufacturers will be better equipped to meet customer demands for faster turnaround times, higher quality, and greater customization flexibility.
4. Additive Manufacturing
Additive manufacturing, also known as 3D printing, holds significant promise for the future of glass manufacturing. Unlike traditional glassmaking processes, which involve melting and shaping glass at high temperatures, additive manufacturing allows for the precise deposition of glass materials layer by layer, using computer-controlled printers. This enables the creation of complex geometries and customized designs that would be difficult or impossible to achieve with conventional methods. Additive manufacturing also reduces material waste and enables rapid prototyping and product iteration, making it ideal for low-volume or customized production runs. While additive manufacturing of glass is still in its early stages, ongoing research and development efforts are expected to unlock new possibilities and applications in the years to come.
5. Integration with Digital Design Tools
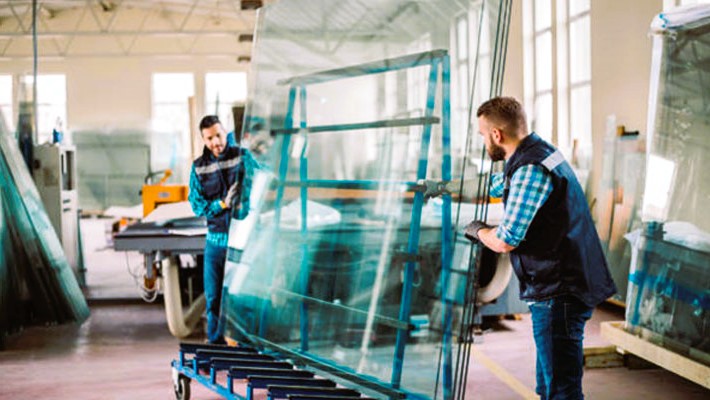
The integration of digital design tools, such as computer-aided design (CAD) software and simulation programs, is transforming the way glass products are conceptualized, designed, and engineered. By leveraging digital design tools, architects, designers, and engineers can create intricate glass structures with greater precision and accuracy, ensuring optimal performance and functionality. Virtual reality (VR) and augmented reality (AR) technologies enable stakeholders to visualize and interact with glass designs in immersive 3D environments, facilitating collaboration and decision-making throughout the design process. The integration of digital design tools with manufacturing processes also enables seamless data exchange and workflow integration, reducing errors and accelerating time to market for new glass products.
The future of glass manufacturing is characterized by innovation, sustainability, and digitalization. By embracing emerging trends and technologies, glass manufacturers can unlock new opportunities for growth, differentiation, and competitive advantage in an increasingly dynamic and competitive marketplace. From sustainable practices and advanced materials to digitalization, automation, and additive manufacturing, the possibilities for innovation in glass manufacturing are virtually limitless. By staying abreast of these trends and investing in research and development, glass manufacturers can position themselves for success and contribute to a more sustainable and technologically advanced future.
For more information on the future of glass manufacturing, please visit Wikipedia.